در صنایع مرتبط با فولاد , سنگ آهن ماده خام اولیه و حیاتی است. برای استفاده از سنگ آهن و تبدیل آن به فولاد و محصولات فولادی چون ( تسمه آهنی – میلگرد – شمش فولادی – تیرآهن – ناودانی – سپری و …) باید ابتدا آن را به کنسانتره (Iron concentrate) و گندله تبدیل کرد و پس از این مراحل فولاد به دست می آید. تولید کنسانتره آهن به اوایل انقلاب صنعتی اروپا باز می گردد وقتی که تقاضا برای فولاد به شدت افزایش پیدا کرد.
کنسانتره آهن چیست؟
کنسانتره پودری است که از سنگ آهن به دست می آید. این پودر کاملا سیاه است و برای بالابردن عیار سنگ آهن های بی کیفیت و با عیار پایین, به آنها اضافه می شود. در واقع کنسانتره یکی از محصولات ثانویه ساخته شده از سنگ آهن است.
از کنسانتره برای تولید گندله آهن, آهن اسفنجی و سایر محصولات فلزی استفاده می شود. دلیل مهمی که باعث می شود این ماده بسیار استفاده شود این است که کنسانتره مواد زائد و مضر ندارد و باعث صرفه جویی در هزینه ها و البته زمان می شود. یعنی سرعت تولید را به شدت بالا می برد.
چه نیازی به فرآوری سنگ آهن است؟
دلایل زیادی وجود دارد که نیاز به فرآوری سنگ آهن را ثابت می کند که از آن جمله می توان به موارد زیر اشاره کرد؛
- اولین دلیل این است که با فرآوری عیار آهن کنترل شده و افزایش می یابد.
- دلیل بعد پاکسازی عناصر مضر و ناخالص سنگ است.
- و در آخر اینکه فرآوری سنگ آهن, ظاهر و داخل سنگ را یکپارچه و یکدست می کند.
نحوه فرآوری سنگ آهن
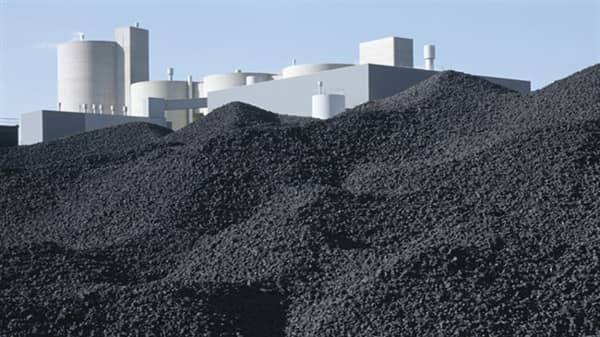
فرآوری سنگآهن براساس محصول تولیدی به دو نوع دسته بندی می شود.
تولید سنگآهن دانهبندی شده
طی این فرآیند که بدون آب و به صورت خشک انجام می شود، با روش مغناطیسی، سنگهای پرعیار و بی کیفیت از یکدیگر جدا می شوند و محصول نهایی به دست می آید. به این محصول سنگ آهن دانهبندی میگویند.
سنگ آهن دانهبندی به دلیل کیفیت پایینی که دارد قابل استفاده در سیستم های احیا نیست ولی به وفور در کوره های بلند استفاده می شود.
تولید کنسانتره سنگآهن
برای ساخت کنسانتره، عیار متوسط سنگ آهن پایین است و برای بالا بردن این عیار، از روشهای مختلف مدرن و پیچیده ای استفاده میشود. در ادامه یکی از این روش ها را توضیح خواهیم داد.
مراحل تولید کنسانتره
برای فرآوری سنگ آهن در صنایع مختلف 4 مرحله وجود دارد که باید طی شود.
- خردایش
- آسیابکنی
- پرعیارسازی
- آبگیری
در کنار این مراحل مواردی مانند واحدهای حمل و نقل, تامین آب مورد نیاز و … نقشی غیر قابل انکار دارند که البته نامی هم از آنها برده نمی شود.
مرحله اول: خردایش
این مرحله زمانی آغاز می شود که ماده اولیه وارد کارخانه می شود و در سنگ شکن قرار می گیرد. تکه های بزرگ سنگ آهن که گاهی تا 100 سانتی متر نیز ابعاد دارند, باید در این مرحله به قطعه های کوچکتر حتی تا ابعاد 20-25 سانتی متر نیز خرد شوند.

در این مرحله لازم است تا ابعاد سنگ های خرد شده یکسان باشد. برای همین در خروجی دستگاه سنگ شکن چیزی شبیه صافی قرار داده شده است که وظیفه غربال کردن سنگ های خرد شده را برعهده دارد. سوراخ های این صافی معادل اندازه های مورد نظر است و فقط سنگ های با ابعاد در نظر گرفته شده از آن عبور می کنند.
سپس نوار نقاله سنگ های خارج شده از سنگ شکن را به مرحله بعد انتقال می دهد. در این مرحله با توجه به اندازه سنگ ها گاهی نیاز است که دوباره آنها خرد شوند. به این مرحله “سنگ شکنی خشک” گفته می شود. در واقع این کار برای جلوگیری از خرد شدن بیش از حد سنگ ها انجام می شود.
سنگ شکنی خشک به شیوه مخروطی انجام می شود و می تواند اندازه سنگ ها را تا 30 میلیمتر کمتر کند.
مقاله پیشنهادی؛ تحلیل صنعت فولاد جهان در سال های آتی
مرحله دوم: آسیابکنی
در این مرحله, سنگ هایی که کمتر از 30 میلیمتر هستند برای خرد شدن بیشتر وارد این مرحله می شوند و به صورت تر شکسته می شوند. این مرحله می تواند با استفاده از آسیاب خودشکن یا نیمه خودشکن یا با استفاده از غلتک های فشاری انجام شود. سنگ هایی که وارد این مرحله می شوند باید به ابعاد ۱-۰/۵ میلیمتر برسند.
محیط خرد شدن این قطعات مرطوب و تر است و اندازه خردایش به وسیله هیدروسیکلون کنترل میشود. به ترکیب نهایی که قطعات خرد شده در آن شناورند، دوغاب یا اسلاری میگویند که توسط پمپ ها قابل انتقال است.
مرحله سوم: پرعیارسازی
پس از مرحله آسیاب که قطعات که به اندازه مورد نظر رسیدند و به قدر کافی ریز و کوچک شدند، برای جداسازی مواد با ارزش از مواد باطله در اسلاری به این مرحله وارد میشوند. همانطور که در مرحله دوم گفتیم, اسلاری به وسیله پمپ به این مرحله انتقال داده می شود. این مرحله را “جدایش مغناطیسی” میگویند.
دستگاههای جداکننده مغناطیسی این مرحله تر و از نوع درام هستند، به این صورت که اسلاری بر روی این درامها (که دارای خاصیت مغناطیسی هستند) عبور می کند و به این ترتیب کانیهای دارای آهن به درام میچسبند و با یک تیغه جمع آوری میشوند و در نهایت سایر کانیها از ته ریز دستگاه خارج میشوند.
جدا کننده های مغناطیسی بر اساس ویژگی ها و خواصی که مواد معدنی دارند دارای انواع مختلفی هستند از جمله؛
- شدت کم
- شدت متوسط
- شدت زیاد
- گرادیان (کمیت عددی) بالا
مرحله چهارم: آبگیری
برای پرعیار شدن سنگ ها در این مرحله روی آنها آبگیری انجام می شود. از آنجایی که سنگ پرعیار در خود آب ذخیره دارد باید خشک و آبگیری شود که این کار توسط فیلترهایی انجام میشود.
در واقع رطوبتی که مناسب سنگهای پرعیار است حدود 9 الی 10 درصد است.
پس از جداسازی و خشک کردن آب کنسانتره، آن را برای دپو کردن به انبار منتقل می کنند. پس از ذخیره کردن کنسانتره آبگیری شده، باطله را برای آبگیری به تجهیزات دیگری که به آن تینکر میگویند، میبرند. در تینکر، مواد سنگین و جامد ته نشین شده و آب از بالای تینکر سرریز میشود، و مواد جامد به کمک بازویی که در کف تینکر وجود دارد به سمت مرکز و سپس با کمک پمپ به سد باطله منتقل میشوند.
گاهی لازم است که سرعت ته نشینی مواد جامد افزایش پیدا کند در این مواقع از ماده ای شیمیایی به نام “فلوکولانت” استفاده می شود. این ماده سرعت چسبیدن ذرات را افزایش داده و باعث سقوط آنها میشود.
گندله چیست؟
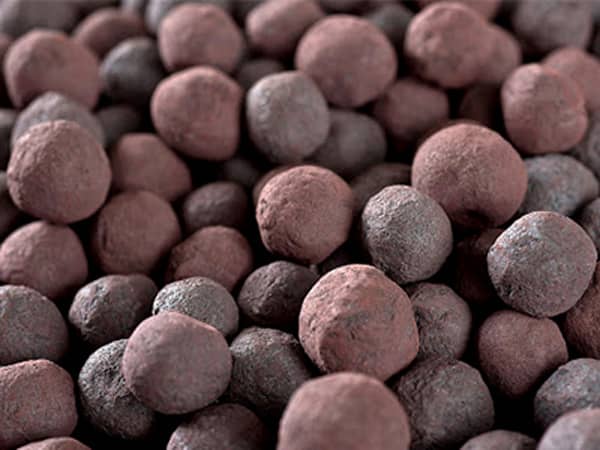
گندله یعنی گلولههایی که از نرمه سنگآهن و سایر مواد افزودنی تولید شده اند. این مواد در ابتدا خام و سپس پخته و سخت شده اند. پس می توان فهمید که سنگ آهن مهم ترین ماده اولیه برای تولید گندله است.
برای تولید گندله خام، از نرمه سنگآهن شامل مواد افزودنی که ۹۰درصد آن زیر ۴۵ میکرون است با محلولهای ترکننده مانند آب برای دستیابی به شکل کروی، در دستگاههای گندله ساز به چرخش درآورده میشوند تا گندله خام تولید شود.
گاهی در حین تولید گندله خام لازم است تا برای بالا بردن کیفیت و خواص متالورژیکی آن موادی مانند هیدروکسید کلسیم به آن اضافه شود.
سپس گندله با ابعاد مورد نظر تولید شده و به سمت دستگاه پخت هدایت می شود.
در مرحله بعد گندلههای خام، به منظور سخت شدن در اتمسفر اکسیدکننده به دقت تا زیر دمای نرم شدن سنگآهن در دستگاهی حرارت داده میشوند تا نخست خشک و سپس پخته شوند، به گونهای که درجه تخلخل آنها کاهش پیدا نکند.
در این مرحله با پیوند بین ذرات سنگآهن و مواد دیگر بار گندله، ساختار بلوری سنگ تغییر پیدا میکند و واکنشهایی بین مواد سرباره ساز و اکسیدهای آهن نیز انجام میشود.
در پایان لازم است تا گندله ها به صورتی خنک شوند که ترک بر ندارند و شکل آنها ثابت بماند.
در حالت کلی گندله ها دارای ویژگی های زیر هستند:
- دارای ابعاد یکنواختی حدود ۹ تا ۱۶ میلیمتر
- تخلخل زیاد و یکنواخت ۲۵ تا ۳۰ درصد
- ترکیب کانیشناختی یکنواخت به شکل هماتیت یا ترکیبات هماتیتدار احیاشونده
- استحکام مکانیکی زیاد و یکنواخت
- مقاومت در برابر سایش
- استحکام مکانیکی کافی در برابر تنش های گرمایی
- قابلیت چسبندگی کم
قیمت کنسانتره و گندله
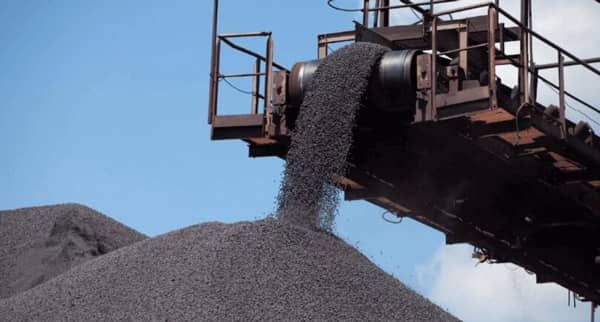
برای آگاهی از قیمت انواع گندله و کنسانتره کافی است با کارشناسان ما تماس بگیرید تا علاوه بر آگاهی از قیمت روز این محصولات, بتوانید برای داشتن خریدی با اطمینان مشاوره دریافت کنید.